-
Giỏ hàng của bạn trống!
In tem decal – Nhãn dán Bình Dương
Giá bán : Liên hệ
In tem decal Bình Dương
In tem decal Bình Dương ứng dụng rộng rãi của nhãn và sự phát triển không ngừng của các loại nhãn đã thúc đẩy sự phát triển của công nghệ in nhãn một cách tự nhiên. In nhãn bao gồm tất cả các phương pháp in như phẳng, lồi, lõm và web, và các điều kiện ứng dụng khác nhau giữa các quốc gia. Tuy nhiên, có thể thấy xu hướng phát triển của nhãn toàn cầu trong những năm gần đây là in flexo, in web hẹp và in kỹ thuật số đã trở thành điểm nhấn mới trong in tem nhãn ở các nước Châu Âu và Châu Mỹ, đồng thời cũng là xu hướng phát triển của in nhãn.
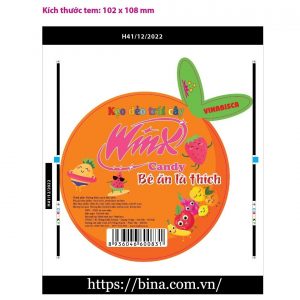
Tình trạng phát triển in tem decal trong nước
Năm 2012, giá trị sản lượng in nhãn của nước tôi là 2 triệu USD, sản lượng là 500 triệu mét vuông, tăng 20% so với cùng kỳ năm trước;
Năm 2013, giá trị đầu ra của việc in nhãn là 8 triệu US và sản lượng đạt 200 triệu mét vuông, tăng 20% so với cùng kỳ năm ngoái. Ngành công nghiệp in nhãn của nước tôi đã đạt được tốc độ tăng trưởng nhanh chóng cùng với sự phát triển của nền kinh tế thị trường, đặc biệt là sự phát triển nhanh chóng của hóa chất hàng ngày, thực phẩm, sản phẩm giặt tẩy, thuốc, mỹ phẩm, đồ gia dụng và thiết bị nhỏ, siêu thị, hậu cần và các ngành công nghiệp khác. Sau vài năm của sự phát triển, chuỗi ngành in nhãn đã được hình thành.
Theo khảo sát, năm 2012, hoạt động xuất bản và bản quyền ở thủ đô sẽ đẩy mạnh chuyển đổi phương thức phát triển, lấy đổi mới cơ chế làm khâu đột phá, tiếp tục đi vào chiều sâu cải cách, đẩy mạnh hội nhập các nguồn lực, đẩy mạnh hội nhập công nghệ cao. ngành xuất bản, đổi mới, hoàn thiện hệ thống dịch vụ văn hóa công về báo chí, xuất bản, tối ưu hóa mô hình quản lý của Chính phủ, nâng cao trình độ phục vụ, phấn đấu tạo ra tình thế mới trong lĩnh vực xuất bản.

Quy trình in tem decal
Tem nhãn sản phẩm bao gồm một số phương pháp in chính, trong giai đoạn tạo bản. Theo các đặc tính sản phẩm khác nhau, chọn các phương pháp in khác nhau và đối với các phương pháp in khác nhau, quy trình tạo tấm cũng khác nhau. Bài viết này lấy quy trình tạo bản in flexo làm ví dụ để giới thiệu ngắn gọn.
Luồng quy trình làm bản in flexo là: bản thảo gốc-phim (phim âm bản)-phơi sáng-rửa-sấy-xử lý hậu kỳ.
- 1. Bản thảo gốc. Thiết kế ban đầu phù hợp để in flexo phải có các đặc điểm sau: một số lượng lớn màu sắc. Nhưng in đè ít hơn, không yêu cầu tái tạo các chi tiết đặc biệt nhỏ, cáp mạng không quá cao nhưng có thể đạt được hiệu ứng in màu, có thể đóng gói trực tuyến.
- 2. Phim (phim âm bản). Nó đáp ứng các yêu cầu của chế tạo tấm, với đồ họa rõ ràng và thông số kỹ thuật kích thước chính xác; sử dụng phim mờ và mật độ của bốn góc của phim phải nhất quán; sử dụng phim chính tả; đo bằng máy đo mật độ truyền, mật độ mức trắng là dưới 0,06; mật độ mức độ màu đen là trên 3,5.
- 3. Phơi sáng bao gồm phơi sáng ngược và phơi sáng chính.
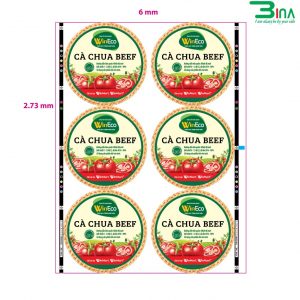
In tem nhãn decal
①Phơi sáng ngược: Màng hỗ trợ của tấm nhựa cảm quang được đặt lên trên và màng bảo vệ được đặt trong ngăn phơi sáng để phơi sáng. Các tia cực tím đi qua màng hỗ trợ để xử lý lớp keo cảm quang. Để thiết lập một lớp nền ổn định, nó cũng có thể kiểm soát độ sâu của quá trình rửa tấm và tăng cường lực liên kết giữa màng hỗ trợ và lớp nhựa cảm quang. Thời gian phơi sáng ngược được xác định bởi độ dày chất nền mong muốn.
②Phơi sáng chính: Còn được gọi là phơi sáng phía trước, tấm phim hỗ trợ tấm nhựa cảm quang hướng xuống dưới và tấm phim bảo vệ hướng lên trên. Đặt phẳng trong ngăn tiếp xúc. Xé màng bảo vệ một lần liên tiếp, sau đó dán mặt phim lên tấm nhựa cảm quang. Đặt màng hút chân không nằm phẳng trên phim (mặt màng không chứa thuốc), hút chân không để màng và lớp nhựa cảm quang được liên kết chặt chẽ. Các tia cực tím đi qua màng chân không và phần trong suốt của màng để trùng hợp và xử lý phần cảm quang của tấm.
Độ dài của thời gian phơi sáng chính được xác định bởi loại tấm và cường độ của nguồn sáng. Nếu thời gian phơi sáng quá ngắn, độ dốc của đồ họa sẽ quá thẳng, các đường sẽ bị uốn cong, các ký tự và dấu chấm nhỏ sẽ bị xóa, nếu không, thời gian phơi sáng sẽ quá dài và chữ viết sẽ bị nhòe. bị mờ. Nếu có những khoảng trống lớn và nhỏ, các đường kẻ dày và mỏng trên cùng một tấm in. Tùy từng trường hợp mà dùng màng đen che và phơi riêng. Các bộ phận nhỏ sẽ không bị mất do giặt để đảm bảo chất lượng của bản in.
4. Rửa sạch: Phần không nhạy cảm với ánh sáng được rửa sạch và hòa tan, và phần cứu trợ quang trùng hợp được giữ lại. Độ dài của thời gian rửa bản được xác định bởi độ dày của bản in và độ sâu của mẫu in.Nếu thời gian rửa bản quá ngắn, nhựa không nhạy quang sẽ còn sót lại trên bản và ảnh hưởng đến độ sâu của việc tạo bản.Nếu thời gian rửa tấm quá lâu, tấm sẽ phồng lên, dẫn đến biến dạng các bộ phận nhỏ hoặc rơi ra.
5. Làm khô: Loại bỏ dung môi rửa bản để bản trở về kích thước và độ dày ban đầu. Nhiệt độ nướng trong khoảng 50-60°C. Thời gian nướng được xác định bởi độ dày của tấm và thời gian rửa, thường là hai giờ đối với tấm dày và một giờ đối với tấm mỏng. Nếu thời gian nướng quá dài và nhiệt độ của tấm nướng quá cao, tấm in sẽ trở nên giòn và ảnh hưởng đến tuổi thọ của bản in. Nếu nhiệt độ nướng quá thấp, thời gian sấy sẽ kéo dài, nếu thời gian nướng quá ngắn, sẽ có những tấm bị mục trong quá trình in.
6. Hậu xử lý: Đó là, detackification và post-exposure. Làm cho nhựa cảm quang cứng lại hoàn toàn (trùng hợp) để đạt được chỉ số độ cứng thích hợp và loại bỏ độ dính của tấm in để tạo điều kiện chuyển mực. Thời gian xử lý hậu kỳ được lấy từ bài kiểm tra và mục đích là không bị nứt hoặc dính.
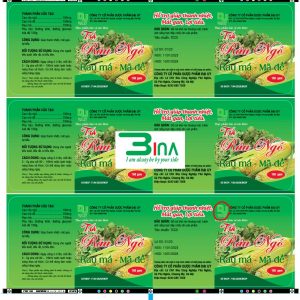
Điều chỉnh mực in tem decal
Với sự phát triển của nền kinh tế, nhãn mác được sử dụng rộng rãi trên các mặt hàng, kéo theo sự phát triển nhanh chóng của ngành in nhãn mác.
Hiểu biết của xã hội về mực in nhãn còn kém xa so với hiểu biết về chất liệu nhãn, phương pháp in… Mực in nhãn giống như một lĩnh vực bí ẩn cần chúng ta nhận biết và khám phá.
Phân loại:
Có nhiều loại mực in nhãn, có thể được chia thành ba loại theo các dung môi khác nhau được sử dụng – mực in nhãn gốc nước, mực in nhãn gốc dung môi và mực in nhãn UV:
- ⑴Mực gốc nước an toàn, hợp vệ sinh, không gây ô nhiễm, đáp ứng yêu cầu bảo vệ môi trường, có lợi cho sức khỏe con người nhưng cũng có những nhược điểm như tốc độ khô chậm, độ bão hòa màu thấp, độ ổn định kém.
- ⑵Mực in nhãn dựa trên dung môi có khả năng thích ứng mạnh với vật liệu nhãn, hiệu suất ổn định và chất lượng in cao; nhưng có vấn đề ô nhiễm môi trường và một số dung môi dễ bay hơi có hại cho cơ thể con người.
- (3) Mực in nhãn UV có hiệu suất tuyệt vời, chất lượng đáng tin cậy và phạm vi ứng dụng rộng rãi; nhưng giá cao, cần có thiết bị sấy đặc biệt và có một số yêu cầu nhất định đối với vật liệu hỗ trợ.
Cân nhắc lựa chọn mực
Khi chọn mực in nhãn, cần xem xét toàn diện một số yếu tố như loại vật liệu in, phương pháp in và điều kiện in, yêu cầu đặc biệt của khách hàng, công nghệ xử lý sau in, sử dụng và điều kiện sử dụng nhãn cũng như chi phí.
Các đặc tính của mực in nhãn chủ yếu bao gồm màu sắc, độ mịn, độ bão hòa, độ bóng, độ bám dính, độ nhớt, độ khô, v.v. Những đặc tính này có ảnh hưởng quan trọng đến quá trình in và chất lượng in.
Nhân tố môi trường: Ảnh hưởng của môi trường xưởng in đến hiệu suất mực và chất lượng in chủ yếu được phản ánh ở hai khía cạnh sau:
- (1) Độ nhớt và độ khô của mực rất nhạy cảm với nhiệt độ môi trường, khi nhiệt độ tăng, độ nhớt của mực giảm, tốc độ khô nhanh hơn, ngược lại, độ nhớt của mực tăng, tốc độ khô nhanh hơn. Chậm hơn. Ngoài ra, độ ẩm xung quanh cũng ảnh hưởng đến độ khô của mực, độ ẩm trong xưởng quá cao không có lợi cho việc làm khô mực, nếu xưởng quá khô sẽ dễ dẫn đến lỗi in do tĩnh điện.
- (2) Việc vệ sinh xưởng in cũng rất quan trọng, vì vậy xưởng in cần được giữ sạch sẽ, không có bụi bẩn, thông thoáng.
Trong quá trình in thường gặp phải các sự cố như độ bền bám mực kém, mực khô kém, lớp mực bám dính, bọt khí, bản dán, bản khô, truyền mực kém, chuyển màu, phân tích các lỗi này như sau:
- (1) Độ bền bám mực kém. Lý do: Sức căng bề mặt của vật liệu in quá thấp, loại mực không phù hợp với loại vật liệu in, hiệu suất của mực kém, v.v. Giải pháp: Xử lý bề mặt vật liệu in, thêm chất làm ẩm để giảm độ căng của mực và thay mực.
- (2) Mực khô kém. Lý do: Tỷ lệ dung môi mực không phù hợp, tốc độ in quá nhanh, độ ẩm xung quanh quá cao, v.v. Giải pháp: Điều chỉnh tỷ lệ dung môi, giảm tốc độ in phù hợp, tăng nhiệt độ sấy, giảm độ ẩm xung quanh, v.v.
- (3) Lớp mực dính vào nhau. Lý do: khô mực kém, mực quá mềm, áp suất in quá cao, độ ẩm xung quanh quá cao. Giải pháp: Điều chỉnh tỷ lệ dung môi mực, thêm một lượng chất chống dính thích hợp, tăng nhiệt độ sấy, giảm áp suất in, giảm độ ẩm môi trường.
- (4) Bong bóng. Lý do: mực chứa không khí, sức căng bề mặt của mực quá cao, độ nhớt của mực quá thấp và tốc độ in quá nhanh. Giải pháp: Thêm lượng chất khử bọt thích hợp, điều chỉnh độ nhớt của mực và giảm tốc độ in một cách thích hợp.
- (5) Bản dán. Lý do: các hạt sắc tố mực quá dày, độ nhớt của mực quá cao, lượng mực quá lớn, áp suất in quá cao, v.v. Giải pháp: thay mực, giảm độ nhớt của mực một cách thích hợp, giảm lượng mực và giảm áp suất in.
- (6) Tấm khô. Nguyên nhân: tốc độ khô mực quá nhanh, nhiệt độ sấy quá cao, tốc độ in quá chậm, v.v. Giải pháp: Điều chỉnh tỷ lệ dung môi mực, giảm nhiệt độ sấy phù hợp và tăng tốc độ in.
- (7) Truyền mực kém. Lý do: Loại mực không phù hợp với loại chất nền, độ nhớt của mực quá cao, có tĩnh điện, v.v. Giải pháp: thay mực, điều chỉnh độ nhớt của mực, thêm chất chống tĩnh điện.
- (8) Pha màu. Lý do: độ lệch của màu mực, tốc độ khô mực không phù hợp, độ ổn định của mực kém, hiệu suất của vật liệu in, thay đổi trong quy trình in, v.v. Giải pháp: thay mực, điều chỉnh tỷ lệ dung môi, điều chỉnh các thông số quy trình in.
- (9) Tĩnh điện. Nguyên nhân: mực quá loãng, tốc độ in quá nhanh, môi trường quá khô, v.v. Giải pháp: thêm chất chống tĩnh điện, tăng độ nhớt của mực, giảm tốc độ in phù hợp, điều chỉnh độ ẩm môi trường.
Trong quá trình in cũng cần chú ý các vấn đề sau:
- (1) Sử dụng cùng nhãn hiệu mực được sản xuất bởi cùng một nhà sản xuất mực để tránh lỗi in do sử dụng lẫn lộn các nhà sản xuất khác nhau và các loại mực khác nhau.
- (2) Mực phải được khuấy hoàn toàn trước khi sử dụng và nên khuấy thường xuyên trong quá trình in để đảm bảo hệ thống mực được phân tán đều.
- (3) Không nên trộn quá nhiều mực mỗi lần và nên tuân thủ nguyên tắc “thêm ít, thêm nhiều”, điều này không chỉ có lợi cho sự ổn định của hiệu suất mực mà còn có thể tránh lãng phí một cách hiệu quả; Ngoài ra, đối với mực spot color cũng cần chuẩn bị tốt Record.
- (4) Trong quá trình in, để đảm bảo chất lượng in nhãn và sản xuất trơn tru, một số chất phụ gia nên được thêm vào mực, chẳng hạn như chất chống tĩnh điện, chất khử bọt, chất tẩy dính, v.v. được kiểm soát trong phạm vi xác định.
Có nhiều thiếu sót trong mực in nhãn ở thị trường Việt Nam, vấn đề nổi bật nhất là vấn đề sai lệch màu mực: một mặt, màu sắc của cùng một loại mực được sản xuất bởi các nhà sản xuất mực khác nhau là khác nhau; mặt khác, thậm chí cùng một loại mực được sản xuất bởi cùng một nhà sản xuất, các lô khác nhau, màu sắc cũng sẽ bị sai lệch, đôi khi còn rất lớn. Vì lý do này, các nhà máy in thường phải ngừng hoạt động để sửa lỗi, điều này rất bất lợi cho sự ổn định của chất lượng in, gây bất tiện lớn cho sản xuất và cản trở nghiêm trọng việc cải thiện chất lượng vật liệu in.
Vẫn còn một khoảng cách nhất định giữa mực trong nước và mực nhập khẩu, đặc biệt là ở các sản phẩm cao cấp, các nhà sản xuất mực trong nước nên nâng cao trình độ kỹ thuật và năng lực sản xuất càng sớm càng tốt để thúc đẩy sự cải tiến của toàn ngành sản xuất mực.
Để đạt được hiệu quả bảo quản tốt hơn, mực in nhãn phải được bảo quản trong hộp kín ở nhiệt độ phòng, trong môi trường mát, khô, tối và thoáng khí.
Trong quá trình bảo quản và quản lý mực in nhãn cũng cần lưu ý một số vấn đề sau:
- (1) An toàn là trên hết, cố gắng tránh xa lửa và nguồn nhiệt khi bảo quản mực để tránh tai nạn.
- (2) Tốt nhất là giữ nhiệt độ ổn định trong kho mực và chênh lệch nhiệt độ so với xưởng in không được quá lớn. Nếu chênh lệch nhiệt độ giữa hai loại lớn, mực nên được đưa vào xưởng in trước, điều này không chỉ có lợi cho sự ổn định của hiệu suất mực mà còn đảm bảo hiệu quả sản xuất cao.
- (3) Ở một số khu vực phía bắc, mùa đông tương đối lạnh, nên tránh bảo quản mực ngoài trời để mực không bị đông lại ở nhiệt độ thấp. Nếu xảy ra hiện tượng keo hóa thì chuyển vào kho có nhiệt độ cao hoặc cho vào nước nóng để khôi phục chất không tan về trạng thái ban đầu.
- (4) Nên tuân theo nguyên tắc “vào trước, ra trước” trong việc bảo quản và quản lý mực, nghĩa là mực mua trước được sử dụng trước, để tránh mực bị ảnh hưởng do tác dụng sử dụng của mực. thời gian bảo quản dài.
- (5) Mực cũng có thời hạn sử dụng nhất định, nếu để quá lâu, các thành phần khác nhau trong mực sẽ bị tách ra và kết tủa. Do đó, mực không thích hợp để lưu trữ lâu dài và thời gian lưu trữ chung là 1 năm.
- (6) Mực còn lại sau khi in phải được đậy kín và bảo quản ở nơi tối, trước khi sử dụng lại phải được lọc bằng lưới lọc hơn 100 mesh, sau khi khuấy đều mới trộn mực mới. Nhà máy in nhãn nên quản lý hiệu quả mực in nhãn, các biện pháp cụ thể là: nhà máy in nhãn nói chung cần thành lập bộ phận quản lý vật tư đặc biệt, chịu trách nhiệm quản lý thống nhất nguyên phụ liệu bao gồm cả mực in, đồng thời thiết lập một bộ phận quản lý hệ thống quản lý vật liệu hoàn chỉnh.Quy trình cho ăn và lấy hàng hợp lý, quy trình xuất nhập kho nghiêm ngặt. Điều đó có nghĩa là, một người đặc biệt chịu trách nhiệm quản lý mực và các sản phẩm mực được lưu trữ ở các khu vực khác nhau để tránh lạm dụng và sử dụng sai.
Ngoài ra, cần lập hồ sơ chi tiết về chủng loại, nguồn gốc, lô hàng, số lượng và cách sử dụng mực để đảm bảo khả năng truy xuất nguồn gốc của sản phẩm.
Chỉnh sửa kết hợp nhiều quá trình in tem decal
Gần đây, in tem decal trong nước chủ yếu áp dụng in letterpress, in offset, in flexo và in lụa, từ góc độ kỹ thuật, mỗi phương pháp in này đều có ưu nhược điểm riêng, không phương pháp in nào có thể thay thế phương pháp in khác.
In offset là phương pháp in tương đối phổ biến, in tờ giấy trong nước về cơ bản là in offset, phương pháp in này có tốc độ cao, độ nét in cao, in đè chính xác, in đầy đủ các lớp nhưng độ bền kém, lớp mực in nhiều. tương đối dày, nhẹ, không thích hợp in các sản phẩm tem nhãn có màu sắc rực rỡ.
In letterpress tái tạo đồ họa với độ rõ nét tốt, tốc độ in cao, độ bền và màu sắc mạnh hơn so với in offset và kém hơn một chút so với in lụa, nhưng mức độ thể hiện và đăng ký mạnh hơn so với in lụa và in flexo, vì vậy việc sản xuất Nhãn trong nước chủ yếu là được thực hiện bằng cách in letterpress.
Ưu điểm lớn nhất của in lụa là lớp mực dày và khả năng che phủ tốt, nhưng tốc độ chậm, hiệu suất cấp kém và mức độ đăng ký thấp (điều này đề cập đến cấp độ chung trong nước), vì vậy máy in lụa có thể được sử dụng để in mà không có cảm giác phân lớp mạnh.
Đặc điểm in của in flexo tương đối trung bình, nước ngoài thường sử dụng phương pháp này để in nhãn, nhưng công nghệ này có yêu cầu cao đối với quá trình xử lý con lăn anilox và trình độ kỹ thuật của công nhân. khá phức tạp, nhãn mác trong nước in theo cách này không nhiều.
Để in các nhãn tinh tế nhất, cần kết hợp hiệu quả các quy trình khác nhau trong quy trình in, tích hợp các ưu điểm của các phương pháp in khác nhau và tạo thành sự kết hợp nhiều ưu điểm hơn.
Mục đích của việc kết hợp nhiều quy trình
Tác dụng chống hàng giả hiệu quả: Việc in ấn với nhiều hiệu ứng công nghệ trên cùng một sản phẩm nhãn, đặc biệt là trên nhãn mỹ phẩm, bao bì thực phẩm rất dễ làm giả, giúp người tiêu dùng chỉ cần nhìn thoáng qua là có thể nhìn thấy sản phẩm thật giả, từ đó bảo vệ được sản phẩm. lợi ích của các nhà sản xuất sản phẩm và người tiêu dùng, đồng thời giành được danh tiếng xuất sắc cho nhà máy in.
Cải thiện chất lượng của vật liệu in: sự kết hợp của nhiều quy trình là kết hợp các ưu điểm của các quy trình in khác nhau
Chất kết dính thường được sử dụng khi in tem deccal
Trong in tem nhãn, keo dán đóng vai trò quan trọng, sau đây giới thiệu các loại keo dán thường dùng trong in tem nhãn
- AF101 Một loại latex acrylic vĩnh cửu có mục đích chung với hiệu suất tuyệt vời trên nhiều vật liệu đóng gói.
- AP103 Một loại latex acrylic vĩnh cửu có mục đích chung với các đặc tính cắt khuôn và loại bỏ chất thải tuyệt vời.
- AP104 Một loại latex acrylic vĩnh cửu có mục đích chung đặc biệt thích hợp cho việc dán nhãn khó.
- AP104A Một loại latex acrylic vĩnh cửu đa dụng, một chất kết dính có độ bám ban đầu và độ bám dính cuối cùng rất cao.
- AP107 Một loại latex acrylic vĩnh viễn có mục đích chung không dễ chảy máu.
- HP103 Chất kết dính gốc cao su vĩnh cửu đa dụng với độ nhớt ban đầu và độ nhớt cuối cùng rất cao.
- HP104 Keo dán gốc cao su vĩnh cửu đa năng với hiệu suất tuyệt vời trên nhiều loại vật liệu đóng gói.
- S1000 Một loại latex acrylic vĩnh viễn có mục đích chung, chất kết dính trong suốt vĩnh viễn.
- S2001 Mủ Acrylic Vĩnh Viễn. Chủ yếu thích hợp cho nhãn phim.
- Mủ Acrylic Vĩnh Viễn S3000. Một chất kết dính trong suốt vĩnh cửu cấp công nghiệp linh hoạt với các đặc tính hiệu suất tuyệt vời.
- S4900 Một loại latex acrylic vĩnh viễn đa năng, một chất kết dính vĩnh viễn đa dụng rõ ràng.
- S692N Một loại latex acrylic vĩnh viễn có mục đích chung. Một chất kết dính mạnh mẽ vĩnh viễn phù hợp với mọi nhiệt độ.
Câu hỏi thường gặp
Khi mọi người nghĩ về thẻ laser, cụm từ “xử lý cẩn thận” chắc chắn sẽ xuất hiện trong đầu vì nó khó sản xuất và vận chuyển. Tất nhiên đó là một sản phẩm tuyệt vời và có rất nhiều nhu cầu về nó. Nhưng nếu bạn có thể thay thế nó bằng các nhãn khác, thì hãy từ bỏ nhãn laser.
Một vấn đề là quá nóng. Đầu nhiệt hạch trên máy in laser đạt tới 250-300 độ F. Để tạo ra một nhãn hoàn chỉnh, đế, chất kết dính và lớp lót phải được lắp ráp. Ngay cả khi nguyên liệu thô được ghép đúng cách, nếu nhãn di chuyển quá chậm trong quá trình in, nhãn sẽ bị hỏng do nhiệt. Một vấn đề khác là nhãn có tai chó – có nghĩa là nhãn vô dụng. Sau khi sản phẩm bị hỏng, cần sửa chữa tại xưởng in.
Các nhà cung cấp và nhà sản xuất giấy phải giải quyết các vấn đề trên trước khi nhãn được chuyển đến người dùng. Nhãn laser thường được xử lý trên thiết bị in flexo quay.
Các nhà cung cấp giấy cần hiểu các yêu cầu kiểm soát độ ẩm cần thiết đối với nhãn laze để có thể giải quyết tình trạng quăn giấy và kẹt giấy. Cho dù hiện tượng viền xảy ra ở 81/2 hay 11 lần cắt bế thì nhà sản xuất cũng sẽ khó giải quyết vấn đề này.
Chất kết dính là một yếu tố khác. Heinl nói: “Nếu nó quá chảy nước, nó sẽ nằm trên trục lăn tích tụ và việc sửa chữa sẽ rất tốn kém.
Trừ khi các lưỡi thích hợp được sử dụng khi cắt tỉa, bụi tích tụ trên xi lanh có thể khiến máy ép bị kẹt. “
Ngoài ra, hãy cẩn thận trên bao bì thành phẩm để tránh gấp nhãn và làm hỏng thông tin của nhà in.
Ưu điểm của nhãn Laser: Nhãn laser có sẵn bằng polypropylene, polyester, giấy và nhựa vinyl. Vật liệu chịu nhiệt đặc biệt và lớp lót chống lật được yêu cầu cho sản xuất. Vì vậy: “Sự lựa chọn rất hạn chế, nhưng mặt khác, nếu bạn sản xuất nhãn truyền nhiệt, sẽ có nhiều loại hơn và sản xuất dễ dàng hơn.” Cả hai nhãn trên đều có thể hiển thị hình ảnh rõ ràng và sống động.
Lợi ích của việc ghi nhãn bằng laze là nó được sản xuất mà không có ruy băng, vì vậy không có vấn đề nhăn ruy băng. Nó chỉ là một loại bột màu hòa tan trong cơ sở.
Nhãn laser ban đầu đắt hơn một chút để sản xuất, nhưng cuối cùng chúng lại tiết kiệm chi phí hơn so với sản xuất nhãn truyền nhiệt. Heinl cho biết: “Bạn có thể sản xuất nhiều cùng một lúc và sau đó bạn cần dừng lại để thay hộp mực (để giảm chi phí, anh ấy chế tạo một chiếc máy ép có chiều rộng 18″ hoặc 20”, có thể in được 2 chiều. “
Phương pháp in ấn nhãn truyền thống
- (1) Các nhãn (đặc biệt là nhãn phim) trên thị trường hiện nay chủ yếu sử dụng phương pháp in lụa và in flexo, không chỉ có công nghệ xử lý phức tạp, thời gian chu kỳ dài mà còn kém kịp thời.
- (2) Về mặt thiết kế sản phẩm, việc lựa chọn các phương án thiết kế đòi hỏi phải kiểm chứng và sửa đổi nhiều lần, điều này không chỉ cồng kềnh mà còn tốn kém.
- (3) Phương pháp in truyền thống sẽ thực hiện in dữ liệu thay đổi và mã hóa kỹ thuật số. Việc in các nhãn hiệu chống hàng giả như mã vạch cần hai hoặc thậm chí ba lần in, cồng kềnh hơn so với in kỹ thuật số.
- (4) Không thể xử lý các công việc ngắn hạn với số lượng in dưới 2.000 bản như nhãn mác, bao bì của một số mặt hàng khuyến mại, sản phẩm dùng thử khiến doanh nghiệp in không những không có lãi mà còn thua lỗ khi thực hiện các hoạt động kinh doanh này.
- (5) Khách hàng ngày càng có yêu cầu cao hơn về chất lượng vật liệu in, nhưng khối lượng in ngày càng nhỏ khiến khả năng cạnh tranh thị trường của in nhãn truyền thống tiếp tục giảm.
Chi phí in tem decal
1. Do không hiểu yêu cầu của khách hàng về hiệu suất của vật liệu in, vật liệu cao cấp đã được sử dụng trong sản xuất, nhưng trên thực tế, miễn là vật liệu trung bình và cấp thấp được chọn, yêu cầu của khách hàng có thể được đáp ứng.
2. Do khách hàng không hiểu rõ công năng của vật liệu nên họ mù quáng đưa ra một số yêu cầu cứng nhắc đối với nhà sản xuất nhãn mác (chẳng hạn như mã số vật liệu theo quy định nước ngoài, v.v.), dẫn đến tăng chi phí không cần thiết. Đối với trường hợp đầu tiên, nhân viên kinh doanh nên tăng cường giao tiếp với khách hàng để hiểu yêu cầu của khách hàng về hiệu suất sản phẩm và các khía cạnh khác, đồng thời để nhân viên kỹ thuật có kinh nghiệm kiểm tra để tránh quá mức cần thiết.
Đối với trường hợp thứ hai, các nhà sản xuất in ấn nên nỗ lực hơn nữa trong việc phối hợp với khách hàng và thuyết phục khách hàng bằng các phương pháp phù hợp, điều này có thể gặp nhiều phản đối nhưng điều rất quan trọng là giảm chi phí.
Ngoài ra, trong trường hợp không có yêu cầu đặc biệt, một số nhà sản xuất in nhãn chọn “vật liệu liên doanh” hoặc vật liệu đã đạt chứng nhận ISO. Lý do họ làm điều này chủ yếu là vì những vật liệu này có hiệu suất tốt hơn, có thể đáp ứng các yêu cầu in nhãn, dễ đạt được thỏa thuận với khách hàng hơn và lựa chọn đơn giản và thuận tiện. Tuy nhiên, để đạt được mục đích giảm chi phí tốt hơn, khi in các loại nhãn khác nhau, có thể sử dụng các loại mực, giấy, nhãn dán và các vật liệu khác để kiểm soát hiệu quả chất thải trong quá trình in nhãn.
Lựa chọn hợp lý phương pháp in
Trước các phương pháp in khác nhau, để giảm thời gian gỡ lỗi thiết bị, nâng cao hiệu quả sản xuất và cải thiện chất lượng sản phẩm ở một mức độ nhất định, để đáp ứng nhu cầu của khách hàng, các nhà sản xuất in nhãn thường sản xuất sản phẩm theo các loại khác nhau và các đợt công việc khác nhau. Sau khi phân loại, chọn các phương pháp in khác nhau để in.
Hiện tại, việc in nhãn của nước tôi chủ yếu là in nổi, in offset và in lụa, trong khi các nước phát triển như Châu Âu và Hoa Kỳ chủ yếu sử dụng in flexo. Với sự cải thiện liên tục của trình độ sản xuất bản in trong nước và việc giảm giá liên tục, chi phí toàn diện của in flexo sẽ giảm đáng kể và các tính năng đầu vào thấp, đầu ra cao của nó sẽ thu hút ngày càng nhiều nhà sản xuất nhãn. Về lâu dài, in flexo sẽ là lựa chọn hàng đầu cho in ấn bao bì, đặc biệt là in tem nhãn.
Hiện nay, trong lĩnh vực in nhãn, in kết hợp ngày càng trở nên phổ biến, một trong những lý do là có thể hoàn thành in và xử lý hậu kỳ cùng một lúc, điều này không chỉ nâng cao hiệu quả sản xuất mà còn giảm đáng kể chi phí của việc in nhãn.
Ngoài ra, sau khi chọn phương pháp in, nếu máy được điều chỉnh hợp lý, cũng có thể giảm lãng phí vật liệu và tổn thất máy móc. Ví dụ: khi in nhãn cao cấp, trước tiên hãy sử dụng giấy bóng đặc biệt thông thường, rẻ hơn để gỡ lỗi máy, sau đó thay thế bằng vật liệu in tốt hơn; khi gỡ lỗi máy, hãy khởi động ở tốc độ trung bình, tiếp đó tăng tốc máy sau khi gỡ lỗi. Sửa màu đồng thời với áp suất tấm, sau đó sửa màu sau khi hoàn thành hai bước này.
Cắt bế sau ép chú ý đến từng chi tiết
Khi sử dụng cắt bế ngoại tuyến, việc cắt bế không chính xác thường xảy ra, thậm chí có thể khiến một số lượng lớn nhãn bị loại bỏ và phải tắt để gỡ lỗi. Nếu người kiểm tra không nắm bắt tốt các tiêu chuẩn cắt bế, điều đó cũng sẽ làm tăng chi phí in ấn.
Ngoài ra, trong quá trình in một số nhãn tự dính (đặc biệt là một số nhãn diện tích nhỏ), hiện tượng bám dính chất thải thường xảy ra trong quá trình cắt nhãn và xả chất thải, đây cũng là một trong những nguyên nhân chính dẫn đến lãng phí in ấn. nguyên vật liệu. Các giải pháp sau đây được đề xuất.
- 1. Khi thiết kế nhãn, hãy tăng diện tích của nhãn một cách hợp lý và hình dạng của nhãn không được quá phức tạp và nên áp dụng cách sắp xếp hợp lý.
- 2. Giảm nhiệt độ của xưởng lưu trữ vật liệu tự dính và xưởng in một cách hợp lý để ngăn độ nhớt của chất kết dính trên giấy bề mặt vật liệu tự dính giảm xuống.
- 3. Thay thế lưỡi cắt đã sử dụng trong một thời gian dài và lưỡi bị cùn, hoặc dán tấm xốp vào giữa tấm cắt và lưỡi cắt, và làm lại tấm cắt. 4. Điều chỉnh áp suất của tấm cắt bế bằng cách đặt tấm đáy cắt bế, sao cho áp suất của tấm cắt bế đồng đều và độ sâu của vết lõm cắt bế phù hợp.
- 5. Cải thiện tốc độ xả chất thải theo khuôn.
Quản lý khoa học và kiểm soát chặt chẽ
Để giảm chi phí in nhãn, ngoài việc nỗ lực nhiều hơn vào từng liên kết quy trình, chúng ta cũng nên tích cực thúc đẩy quản lý kỹ thuật số và tiêu chuẩn hóa. Các doanh nghiệp in nhãn trong nước nên thiết lập các khái niệm quản lý mới và thiết lập một hệ thống quản lý mới đồng thời giới thiệu thiết bị mới, quy trình mới và công nghệ mới để cải thiện toàn diện chất lượng sản xuất nhãn và giảm chi phí bằng quản lý khoa học và tiêu chuẩn hóa.
Xác định yêu cầu sản phẩm—xem xét yêu cầu sản phẩm—chuẩn bị sản xuất—lập kế hoạch sản xuất—thực hiện sản xuất sản phẩm—kiểm tra thành phẩm—giao sản phẩm
Nói tóm lại, một chế độ quản lý khoa học có thể kết hợp một cách hữu cơ các bước quy trình sản xuất nhãn khác nhau để thực hiện kiểm soát tổng thể quy trình sản xuất. Giảm chi phí in nhãn là một nhiệm vụ tổng thể và điều quan trọng là lập kế hoạch tổng thể hợp lý trong giai đoạn thiết kế trước khi in, có tính đến đặc điểm quy trình của từng quy trình và kiểm soát hợp lý toàn bộ quá trình in nhãn thông qua quản lý khoa học, để đảm bảo chất lượng đồng thời giảm lãng phí.
Trong suốt quá trình sản xuất công ty TNHH Quốc Tế BiNa Việt Nam, sự phối hợp giữa nhà sản xuất in nhãn và khách hàng cũng xuyên suốt, ảnh hưởng đến mọi mắt xích của quá trình in nhãn. Đối với những khách hàng đưa ra yêu cầu rõ ràng, các nhà sản xuất in nhãn nên cố gắng hết sức để điều phối mối quan hệ giữa sản xuất và yêu cầu của khách hàng theo tình hình thực tế của nhà máy và giảm thiểu chi phí in nhãn.
Chỉ những khách hàng đã đăng nhập và mua sản phẩm này mới có thể đưa ra đánh giá.
Đánh giá
Chưa có đánh giá nào.